Green hydrogen is an emerging decarbonisation vector for the global economy and a key technology for decarbonisation of heavy-duty transport, heating, industry, feedstocks, and long-duration energy storage. It is classified as ‘green’ if it uses electricity from renewable sources (e.g. wind and solar) to produce hydrogen via electrolysis of water.
A recent report (1) suggests that up to 38 million tonnes per annum (Mtpa) of clean hydrogen is expected to come into production by 2030, including 25Mtpa of green hydrogen. This is a dramatic increase on where we are in early 2024, with less than 1Mtpa of clean hydrogen production in operation. It is anticipated that this target may increase as a result of recent subsidies including a $7 billion stimulus package for regional clean hydrogen hubs announced by the US Department of Energy (DOE) in November 2023. Similar financial support, including EU green hydrogen auctions and the UK’s Contracts for Difference tenders may contribute to an increased target, with other countries including India, China, Australia, Japan and South Korea announcing tax incentives for green hydrogen production.
The intention of these global incentives is to make large-scale green hydrogen projects bankable. In May 2023 Neom took Final Investment Decision (FID) on a $8.4 billion green hydrogen and ammonia project in Saudi Arabia which has a Commercial Operations Date (COD) in 2026. With Gigascale green hydrogen production finally becoming a reality, and with the promise of increasing levels of fiscal support, will we see an uptick in FIDs in 2024?
There still remains a substantial gap between project announcements and what is required, with 75Mtpa of clean hydrogen needed by 2030 to achieve net-zero targets. The challenges associated with bridging this gap include lack of clarity on how subsidies will be implemented, long term offtake agreements, manufacturing costs vs incumbent fossil-based hydrogen, EPC contractor capacity, risk appetite and capability, technology risk and permitting complexity. These factors are important to the insurability of green hydrogen, and one of the significant risks is that of scale-up of manufacturing capacity for electrolysers, wind turbines and PV panels to meet this nascent demand.
There are four major technologies for green hydrogen production: Alkali Water Electrolysis (AWE) and Proton Exchange Membrane (PEM) are already in commercialization, whilst Anion Exchange Membranes (AEM) and Solid Oxide Electrolysis Cells (SOEC) are still in a pilot/early commercialization phase. Global electrolyser manufacturing capacity reached almost 11GW in 2022 with alkaline designs accounting for 85% and PEMs for less than 15%. The deployment of all the projects in the current pipeline will require a 15-30-fold increase in installed electrolyser capacity of 170-365 GW by 2030, equivalent to new manufacturing facilities (Gigafactories) with a combined capacity of around 22-50 GW per year, being added every year between 2024 and 2030, building fast and at massive scale from a very low baseline.
This has created a ‘chicken and egg’ dilemma, with manufacturers building production capacity in anticipation of a surge in electrolyser orders in 2023, which have not materialized due to FID delays and project cancellations. As a result, there has been significant reduction in the profitability and share price of many ‘Tier 1’ Original Equipment Manufacturers (OEMs), with several of these at high Risk of Financial Distress (RFID) as a consequence (4,6). In the inevitable consolidation of the industry over the coming years, successful OEMs will be those who can produce high performance products at mass-scale from a low-cost base, with the ability to re-tool production lines in response to demand.
As a result, OEMs are upscaling their electrolysis stack and systems design (larger cells, more cells/stack, improved cell performance) and building Gigafactories (numbering up) to increase production volumes and improving production technologies, e.g. through use of robotic assembly.
Electrolyser Scale-up
Both PEM and AWE electrolysers are considered mature products. A 165MW AWE plant was constructed in1927 at Rjukan Norway, making use of low-cost hydroelectricity to generate hydrogen for ammonia production, whilst PEM was first developed in the 1960s by GE for spacecraft applications. Additional improvements and technical innovations are required for Gigascale hydrogen production. This scale-up in electrolyser size/capacity has been most pronounced for PEM units as seen below for the Siemens Silyser portfolio.
Scale-up allows simplification of balance of plant (BOP) equipment and is primarily achieved by increase in current density by reducing ohmic resistance, larger cell sizes and more cells per stack. This scale-up requires management of new risks including membrane durability, manufacturing complexity including production line limitations, cell testing, thermal and hydraulic management of larger stacks.
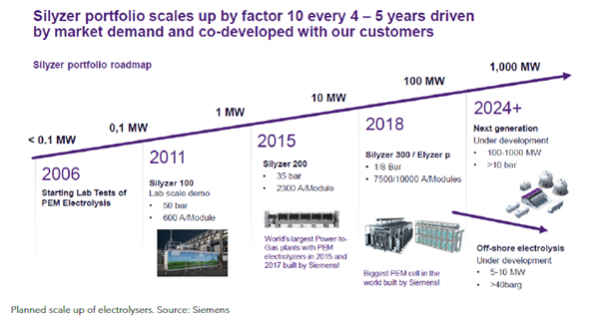
Mass Production Challenges – Emerging Risks of Gigafactories
ITM Power completed the world’s first Gigafactory for electrolyser production in January 2021 in Sheffield, UK. The factory took two and half years to build at a cost of ~£50 million, including land acquisition, construction, machinery and fit-out, with production capacity ramp-up to 60 stacks per year (300 MW/year) by 2023 and 200 stacks (1 GW/year) by 2025.
There has been a flurry of new Gigafactory announcements by other OEMs since then, mainly for PEM and AWE manufacture. Each Gigafactory has a unique design and assembly process, and therefore unique risk profiles. The most fundamental of these relates to alternative approaches to electrolyser manufacture. One is stack production from the ground up using imported raw materials –from cutting and machining of the plates, to welding, nickel plating and assembling of the stack cells and membranes, and final assembly in one of the stacking assembly lines. Some manufacturers continue to use manual processes for stack construction and assembly.
Others are relying on multiple vendors to produce specialised materials or bespoke and small volume sub-components, which make it difficult to achieve cost reductions or control quality. Still others are engaging with machine builders on alternative assembly processes and factory tooling. Again, some OEMs are focusing on stack manufacture only, whilst others are assembling entire electrolyser modules.
According to The International Renewable Agency (IRENA), the economies of scale achieved through moving assembly from a manual to a fully automated process, and through standardisation of designs can reduce stack costs by 60-70%, with more efficient production, improved build quality, reduced labour costs and less wastage. Existing semi-automatic assembly lines for PEM Fuel Cell (PEMFC) manufacture provide a useful learning for set-up, automation and scale-up of electrolyser technology to GW scale. As with PEMFC manufacture, PEM electrolyser production will be split into four separate production lines (Membrane Electrode Assembly, Catalyst Coated Membrane, BiPolar Plate and finished stack). A summary of existing and some emerging manufacturing technologies is provided in the table below(3).
Several OEMs are developing Gigafactories while still evaluating options for each individual manufacturing step, with alternative processes under evaluation for catalyst coating including decal and spray coating. It will be a learning curve until standardisation of components and processes is achieved. One approach to both component manufacture and to emerging automation technology for factory tooling is to outsource initially to deliver learnings in both mass production and quality then bring ‘best in class’ production in-house. In the near-term there will be a trade-off between implementing fully automatic production lines and delivery time. While high volume production can achieve reductions in unit costs for electrolyser plus stack, that can be wiped out by a few months delay in start-up (DSU) and associated project financing costs.
Additional risk mitigations for large electrolyser volume production include adequate quality assurance/control (QA/QC) for manufacturing processes and procedures. OEMs also need to pay attention to QA/QC in the component and stack manufacturing process. For instance, a technology known as Reactive Impinging Flow is used in the PEMFC industry to check and record defects present on the CCM substrate(2). . Material test certificates (MTC) will also need to be maintained for the complete production process.
Detailed Factory Acceptance Testing (FAT) for completed electrolysers are required. This can be performed in an ATEX-rated location within the Gigafactory provided sufficient power supply is available. FAT typically considers steady state operation of electrolysers including turndown performance. With a small number of high-profile product recalls over the last 12 months, Accelerated Lifetime Testing (ALT) and Accelerated Stress Testing (AST) of electrolyser stacks should also be considered, using aggravated conditions to reveal faults and modes of failure in a short amount of time. Some OEMs are also assessing the feasibility of factory testing each cell before stacking and assembly, which would result in higher reliability and less wastage.
The China Syndrome
China plays host to many low-cost AWE manufacturers, but local industry newcomers are also focusing on PEM technology while some innovators are building industrial scale SOEC and AEM electrolyser manufacturing capacity. Current forecasts estimate China will reach 40GW of electrolyser manufacturing capacity by 2030 from 0.8GW in 2022. This will far exceed Chinese domestic demand and so it is expected that many global green hydrogen projects will utilise Chinese electrolysers. There is also a real risk that Chinese-built electrolysers will dominate the market, in the same way that Chinese solar panels did in the 2010s, destroying the European PV manufacturing sector in just a few years.
Siemens, Thyssenkrupp and Cummins are all investing in manufacturing capabilities (Gigafactories) in China in joint venture with Chinese firms. The world’s largest electrolyser was manufactured by Belgian company John Cockerill in China in a joint venture (Cockerill Jingli). By building in China, the industry is seeing shortened construction times and a cost advantage compared to Europe and the US. This decision is also driven by supply chain vulnerabilities including securing supply of critical materials for electrode catalyst production, which will be exacerbated as global electrolyser production scales up. Delay in Start-Up (DSU) risks will be higher for Western OEMs as a result.
China can produce all key parts domestically with few exceptions (notably hydrogen valves). Design of electrolysers may vary depending on location in terms of durability, efficiency and reliability, especially for large systems. There have been some recent major performance issues noted with Chinese electrolysers – the Sinopec 260MW Kuqa green hydrogen project (5), which includes electrolysers supplied by 3 different Chinese OEMs, has been operating at less than a third of its installed capacity due to various factors, including poor turndown performance, high hydrogen crossover and low efficiencies. Although the root causes of this have not been made known, there are undoubtedly lessons to be learned regarding improved QA/QC, gap analysis on codes and standards and robust FAT of complete systems.
Conclusion
- In order to meet the expected ramp-up in green hydrogen production capacity anticipated over the next decade, significant upscaling of electrolyser capacity will be required, both in terms of scale-up (size) and numbering up (unit count), both of which are necessary to achieve economies of scale.
- Scale-up of electrolyser capacity introduces a new set of risks, for the manufacturing processes involved, design and durability of sub-components including membrane electrode assemblies, and for thermal and hydraulic management processes in the stack.
- Mass production of electrolysers in new Gigafactories will introduce complex risks associated with bespoke high throughput equipment and automation of assembly processes, some of which insurers will view as prototypical. Critical, high value, sensitive machinery is a significant BI exposure. The risks presented in this report show that ‘not all Gigafactories are created equal’. Lessons can be learned from the hydrogen fuel cell industry and from Gigafactories for battery manufacture, to assist with risk allocation.
- Based on recent performance issues, particular diligence should be exercised from developers using Chinese-manufacture electrolysers in their projects. Rigorous QA/QC of the entire manufacturing process may be requirement imposed by, including FAT and Accelerated Lifetime/Stress testing of completed units.
References:
Hydrogen Insights, May 2023, Hydrogen Council, McKinsey and Company